Seymour Snerd
Lifetime Supporter
One difference I think I see between mine 2160 and Jim's 2264 is that along the line where Jim's broke, mine has tack welds/brazes top and bottom, and I don't see those, or evidence of them, on Jim's (where the red arrows are below).
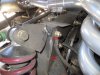
Without those, that side piece that broke goes a long way inward, toward the center of the car, before it's attached to anything.
It's a very difficult area to visualize because over most of its area it's two layers thick, but the two layers aren't connected to each other in very many places. But th the U-shaped shell in which the shock upper mount is bolted is just one layer of 22-gauge steel, and on it's own would be quite flexible. Only the sides of the U are connected; the "top" of the U is just a bridge.
That's why I think it depends on the bolt and the shock eye for rigidity. And even with that the anti-roll bar might be flexing it a lot. One thing I'm tempted to do with mine is simply close the bottom of the U so it's a box. And maybe connect the top of the U to what's behind it.
Sure wish I had a "real" one to look at....
I wonder if one of our Mirage-owning friends, or Andrew K, would take some pictures for us...
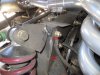
Without those, that side piece that broke goes a long way inward, toward the center of the car, before it's attached to anything.
It's a very difficult area to visualize because over most of its area it's two layers thick, but the two layers aren't connected to each other in very many places. But th the U-shaped shell in which the shock upper mount is bolted is just one layer of 22-gauge steel, and on it's own would be quite flexible. Only the sides of the U are connected; the "top" of the U is just a bridge.
That's why I think it depends on the bolt and the shock eye for rigidity. And even with that the anti-roll bar might be flexing it a lot. One thing I'm tempted to do with mine is simply close the bottom of the U so it's a box. And maybe connect the top of the U to what's behind it.
Sure wish I had a "real" one to look at....
I wonder if one of our Mirage-owning friends, or Andrew K, would take some pictures for us...
Last edited: