I am still plagued with two issues that I can't get a handle on. The first is a long standing one of the alternator overheating. It now is doing it intermittently. Last week I was working on the second problem of the clutch not releasing. The engine was running fine for about 15 minutes. I shut it down to readjust the linkage to the shifter and the clutch. When I started it back up the belt began smoking almost instantly. I have redone all the major ground connections at the battery, the block, and frame, as I suspected the block ground when it first started many moons ago. That ground is coming off the trans adapter which is aluminum. I scuffed up the ground strap connections as well as where they go to the frame, which is the cross member across the back of the engine. Now that bar is ceramic coated, and I don't know the merits of ceramic coating for a ground location, so I roughed it up with sand paper as well. It needs to be redone since several mods following the coating process. All the battery leads from the electronics posts were snugged up. I managed to get the engine to run for about 3-4 minutes before the belt began smoking. The belt feels snug, but I can see it flexing some when the motor is running, so I will tighten it up just for good measure and see.
Concerning the clutch, I think now it has come down to the wrong size of master cylinder. With a full pedal throw the slave is moving a mere 5mm. It needs to travel approximately 13. So I will go beck to my collection of MCs and try it again. My problem is that I can't get any figures on the size of the slave. So Its the old try it and see. The feel of the pedal is hard, so it is taking too much pressure to get the little movement out of the slave. The Master that is in there now is a 5/8" unit. Any suggestions would be greatly appreciated.
On other fronts, I have mounted the canards and they look great. They are scuffed up aluminum for now. I will either leave them this way or polish them.
Bill
Concerning the clutch, I think now it has come down to the wrong size of master cylinder. With a full pedal throw the slave is moving a mere 5mm. It needs to travel approximately 13. So I will go beck to my collection of MCs and try it again. My problem is that I can't get any figures on the size of the slave. So Its the old try it and see. The feel of the pedal is hard, so it is taking too much pressure to get the little movement out of the slave. The Master that is in there now is a 5/8" unit. Any suggestions would be greatly appreciated.
On other fronts, I have mounted the canards and they look great. They are scuffed up aluminum for now. I will either leave them this way or polish them.
Bill


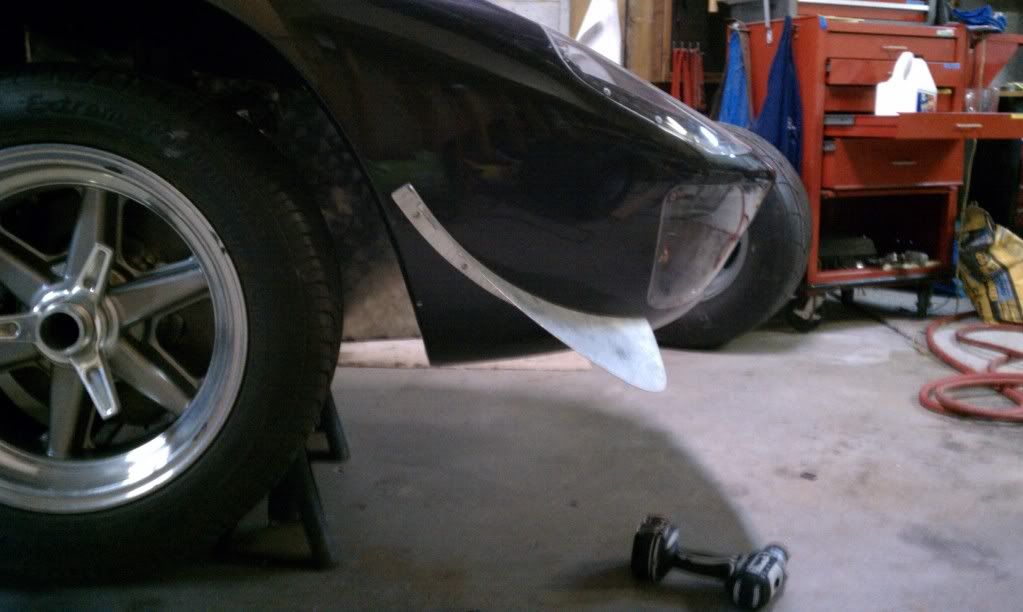