Hi Kim,
With the learning curve required to complete a car of this caliber, the support and knowledge base available from this forum is invaluable to the home builder.
Having to take something apart and do it all again is not unusual as individual car owners have full choice of parts they want resulting in combinations the kit manufacturer could not predict or tool up for.
Things are pretty tight down in the foot box of a GT40 so your "difficult to get pics of the pedal box" comment is spot on. Here's a pic of an early RCR pedal box with the clock spring referred to earlier.
Cheers
Ian
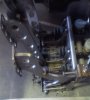
With the learning curve required to complete a car of this caliber, the support and knowledge base available from this forum is invaluable to the home builder.
Having to take something apart and do it all again is not unusual as individual car owners have full choice of parts they want resulting in combinations the kit manufacturer could not predict or tool up for.
Things are pretty tight down in the foot box of a GT40 so your "difficult to get pics of the pedal box" comment is spot on. Here's a pic of an early RCR pedal box with the clock spring referred to earlier.
Cheers
Ian
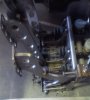