Roger Reid
Supporter
Joel. Your on the right track. Ever considered skinning your welded aluminum structure? Possibly make your prototype from Styrofoam with aluminum tubing at each end for connections then skin it and remove the Styrofoam?
I'm doing something similar. I machined adapters for each end. Then split a 4" aluminum 90 degree bend on the sides. Cut, weld, and beat it with a hammer to make it fit. Doing it in cadd only helps visualize how you are going to beat on it.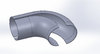
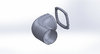
I'm doing something similar. I machined adapters for each end. Then split a 4" aluminum 90 degree bend on the sides. Cut, weld, and beat it with a hammer to make it fit. Doing it in cadd only helps visualize how you are going to beat on it.
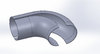
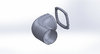