Spaghetti Time... AKA Wiring
After wrapping up all of the plumbing work it was time to dive in to the most time consuming part of the build thus far, the wiring. I utilized the included harness from Ron Francis (Bare Bonez kit) but I added quite a few relays to the system. I added three fuel pump relays, two fan relays, as well as a relay system for the headlights. I purchase all of my switches from Ron Francis as well going with the Synergy billet style switches throughout. Additionally, I'm running the Digital Guard Dawg keyless ignition on my vehicle.
So, I had to incorporate all of these systems together:
Standard Harness
Edelbrock Pro Flo 4 Harness
Three Fuel Pump Relays
Headlight Relays
Fan Relays
Vintage Air System Wiring
Digital Guard Dawg System Wiring
Additional 6 Circuit Fuse box for Switches
I started by setting the dash in place to determine where I wanted to mount the main fuse box, Digital Guard Dawg box, and additional 6 circuit fuse box. I ended up mounting the main fuse box above the passengers feet and the ignition box and smaller fuse box above the drivers feet. Both are fairly easy to access if necessary. From this point it was just a matter of running the wires where they need to go and incorporating the relays, switches, etc. I worked on this for several weeks for short increments, just tackling one or two things per session until I had wrapped it up. I also built out all of the battery cables at this time and mounted a power distribution block in the area near the battery behind the passenger seat. From the distribution block the fuel pump and other relays draw their power. Each of the fuel pump relays is mounted close to their respective pump so one is behind the passenger seat and the other two relays are behind the drivers seat. The PCM for the Pro Flo Systme is mounted midway down the tunnel behind the passenger seat along with it's relay and fuse. All of the other relays are behind the dash close to the main fuse box. During the time I was working on the wiring the addition of Reincarnation magazine featuring Chuck and Ryan's RCR 40 came out. I noticed they had small fans to the access panels in the engine compartment as a way to circulate air. Since I was in the middle of wiring my car, I quickly ordered the fans an additional relay, and switch and installed them as well.
I have a total of 9 switches on the switch panel and they are in the following order from left to right:
Left Low Pressure Fuel Pump
Engine Compartment Fans
Wiper Switch
Turn Signal
Hazard Lights
Horn
Headlights (w/ high beam built in)
Unassigned / Extra
Right Low Pressure Transfer Pump
I made weather tight connectors for all of the switches so that each switch panel can be quickly and easily removed. Also, I did not like the included Vintage Air controls so I upgraded to their billet version, it matches my switches much better. Initially I thought that I would be able to fit this into the switch panel along side the other switches and this idea failed miserably as their was not enough depth due to the angle the switch panel is mounted at, so I made a nice bracket out of angle aluminum and mounted them centered under the dash.
From looking back at the photos I started this on October 2 and was able to test all of the electrical components on November 29. So it took me about two months of incremental work to complete the electrical system.
"Success is the sum of small efforts, repeated day in and day out." -Robert Collier
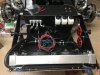