Shaun
Supporter
Hi all
So finally the build has started, took delivery of the chassis last week, spent a while unpacking all the panels, checking bits, putting back whats not needed yet and off I go on the journey so many of you guys have done. Mind you some great support thus far from SGT and Mick plus I am lucky to it seems be close to many great resources like Frank and Paul.
Getting a set of stands off Paul (PaulBav) now his 40 is road legal (well almost!!) this Saturday but at present its the floor pan being sorted, may be being a bit OCD filing to make it fit 100% spot on for a part that few apart from the odd run over squirrel will ever see but devil in the detail, as my mentor said, "If its worth doing lad do it properly".
So workshop ready, did treat myself to a new Teng toolkit, have amassed a few tools over the years but its only when you look hard you see many are old, worn out and past it, much like I feel most mornings. Think I got carried away mind, went for the big monster one, still will see me out so worth every penny.
Also have a bit of light relief should I get stressed, pinball restoration always been a hobby along with jukeboxes, although that has to go as well, going to be morphed into a GT40 part of some sort, gearbox maybe?
So I'll post as much as I can, ask questions, have a laugh, get some input and thoroughly enjoy the whole process.
First question though, not sure why the image upload rotates my images through 90 degrees? Is it because they are not square? That ain't bad, question 1 and its not even about the 40
Cheers
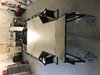
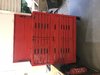
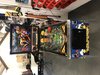
So finally the build has started, took delivery of the chassis last week, spent a while unpacking all the panels, checking bits, putting back whats not needed yet and off I go on the journey so many of you guys have done. Mind you some great support thus far from SGT and Mick plus I am lucky to it seems be close to many great resources like Frank and Paul.
Getting a set of stands off Paul (PaulBav) now his 40 is road legal (well almost!!) this Saturday but at present its the floor pan being sorted, may be being a bit OCD filing to make it fit 100% spot on for a part that few apart from the odd run over squirrel will ever see but devil in the detail, as my mentor said, "If its worth doing lad do it properly".
So workshop ready, did treat myself to a new Teng toolkit, have amassed a few tools over the years but its only when you look hard you see many are old, worn out and past it, much like I feel most mornings. Think I got carried away mind, went for the big monster one, still will see me out so worth every penny.
Also have a bit of light relief should I get stressed, pinball restoration always been a hobby along with jukeboxes, although that has to go as well, going to be morphed into a GT40 part of some sort, gearbox maybe?
So I'll post as much as I can, ask questions, have a laugh, get some input and thoroughly enjoy the whole process.
First question though, not sure why the image upload rotates my images through 90 degrees? Is it because they are not square? That ain't bad, question 1 and its not even about the 40

Cheers
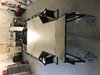
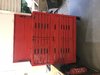
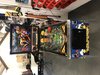