Thanks Michel, but don't hold your breath, everything takes me ages.
In further news, now that the scuttle is out of the way, a friend helped me pull the tail mold off what is left of the pattern.
We bolted it tougher roughly to get an idea of the scale of the next step. It's a big part, the surface area is over 6 m2. Now to get on with preparing this. Some more return fences to make, then more polishing, matt cutting etc etc.
My gell coat application does not look so good when the rear panel is backlit in the open door like that
Feels like I've come a long way since I bought the model to copy!
Cheers
Fred W B
In further news, now that the scuttle is out of the way, a friend helped me pull the tail mold off what is left of the pattern.
We bolted it tougher roughly to get an idea of the scale of the next step. It's a big part, the surface area is over 6 m2. Now to get on with preparing this. Some more return fences to make, then more polishing, matt cutting etc etc.
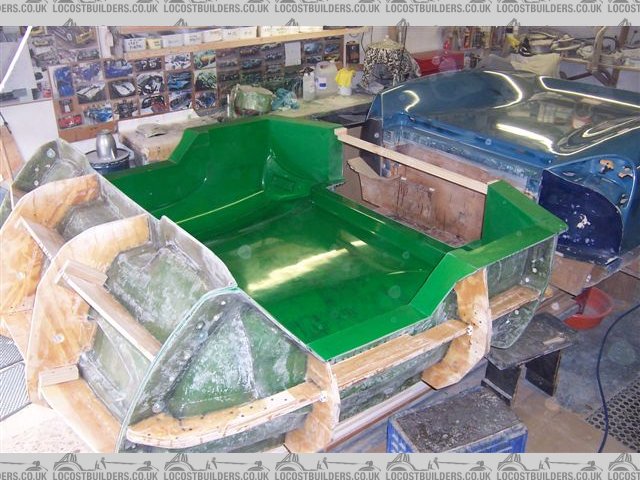
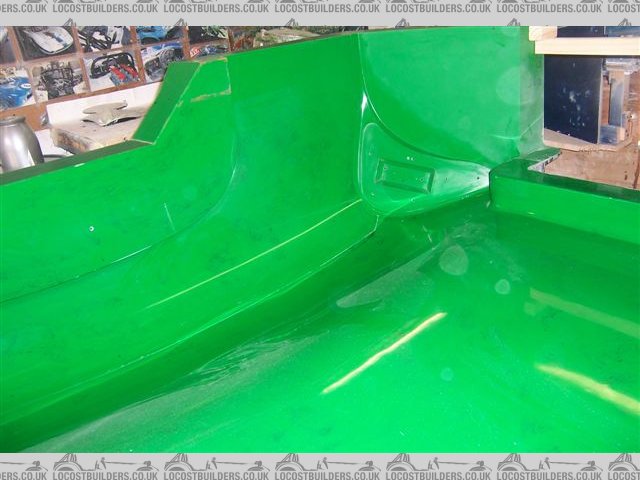
My gell coat application does not look so good when the rear panel is backlit in the open door like that
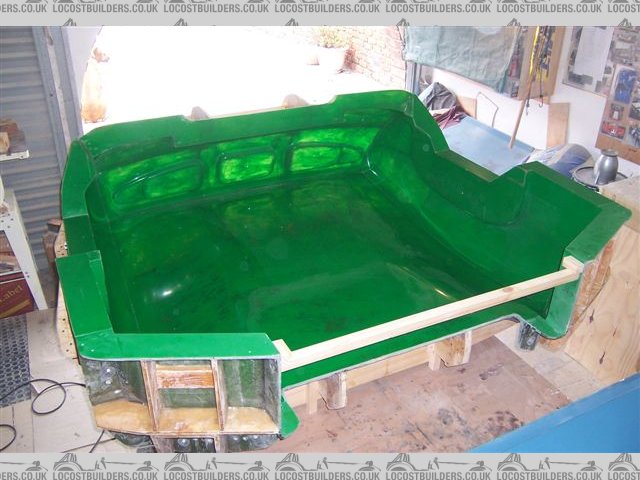
Feels like I've come a long way since I bought the model to copy!
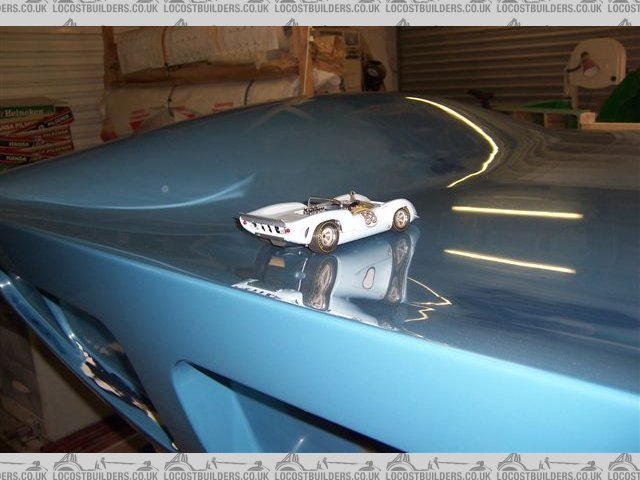
Cheers
Fred W B
Last edited: