INSTALLING THE RADIATOR FANS.
I had a friend o mine welding 4 additional tabs to the radiator. They are app 100mm wide and deep.
Sven my CNC friend made me some nice aluminium nuts and spacers fitting exactly in the slot recess of the fan. Mounting the whole assembly with elastic elements was done quickly.
One thing: I think the fans work most efficient if the shroud of them seals tight to the radiator, in order to avoid any "false" air is sucked in from the side ( if one would mount them with a certain distance to the radiator surface). I used 2mmm selfadhesive foam to create a seal between the fan and the radiator. The mounting elements are than adjusted in a way, that they provide a little positive pressure on this foam seal.
Mounting elements
installed on the fan
foam stripe seal
Welded Tab and installed fan
completely assembled
TOM
AWH : 568 h
I had a friend o mine welding 4 additional tabs to the radiator. They are app 100mm wide and deep.
Sven my CNC friend made me some nice aluminium nuts and spacers fitting exactly in the slot recess of the fan. Mounting the whole assembly with elastic elements was done quickly.
One thing: I think the fans work most efficient if the shroud of them seals tight to the radiator, in order to avoid any "false" air is sucked in from the side ( if one would mount them with a certain distance to the radiator surface). I used 2mmm selfadhesive foam to create a seal between the fan and the radiator. The mounting elements are than adjusted in a way, that they provide a little positive pressure on this foam seal.
Mounting elements
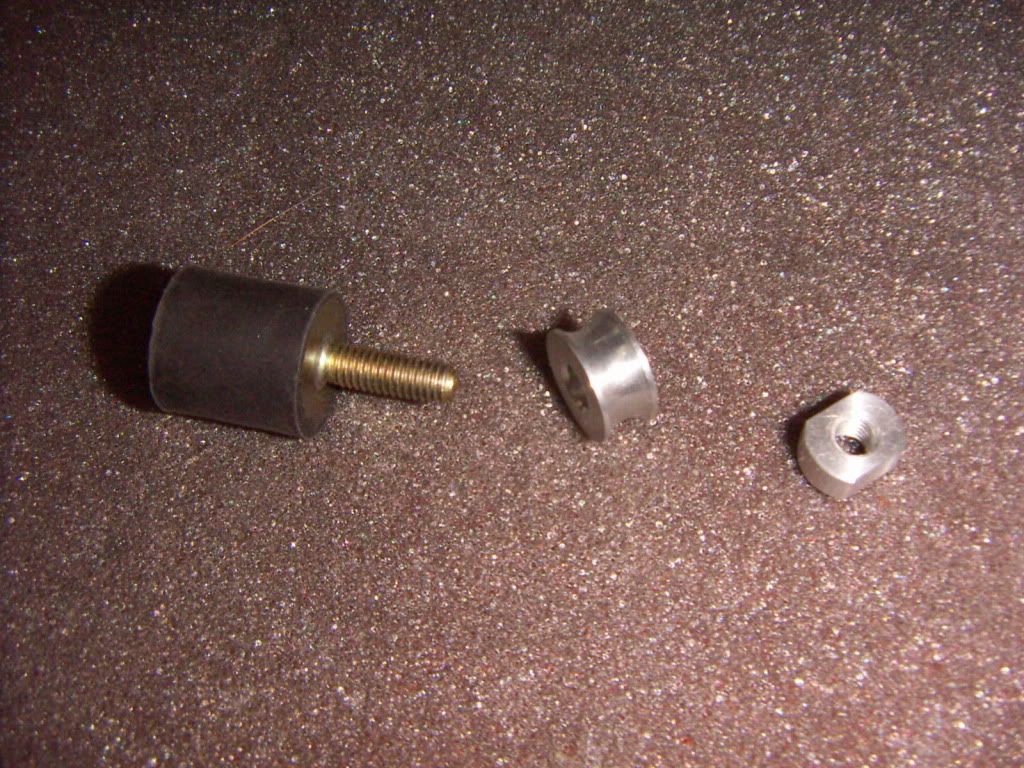
installed on the fan
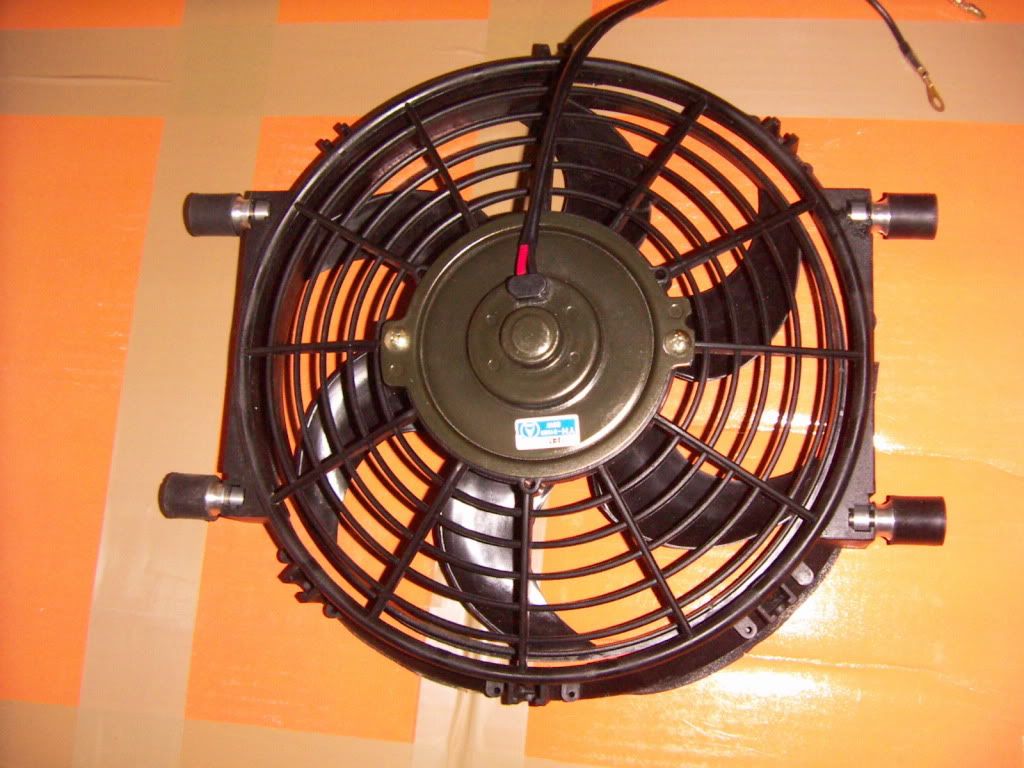
foam stripe seal
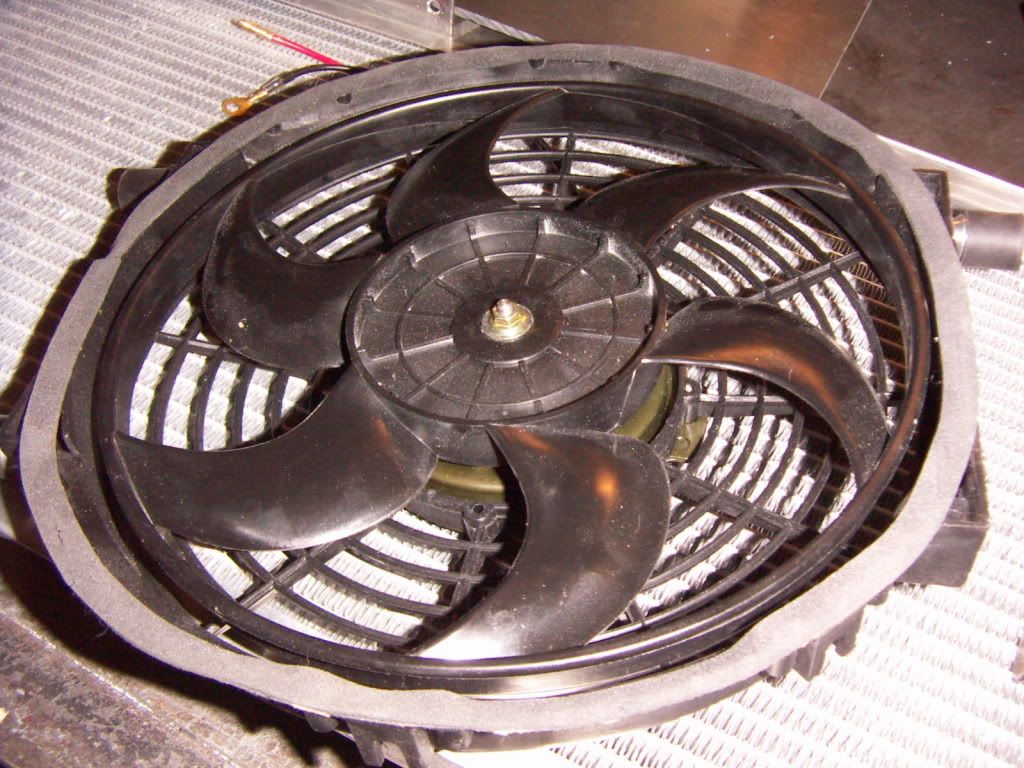
Welded Tab and installed fan

completely assembled
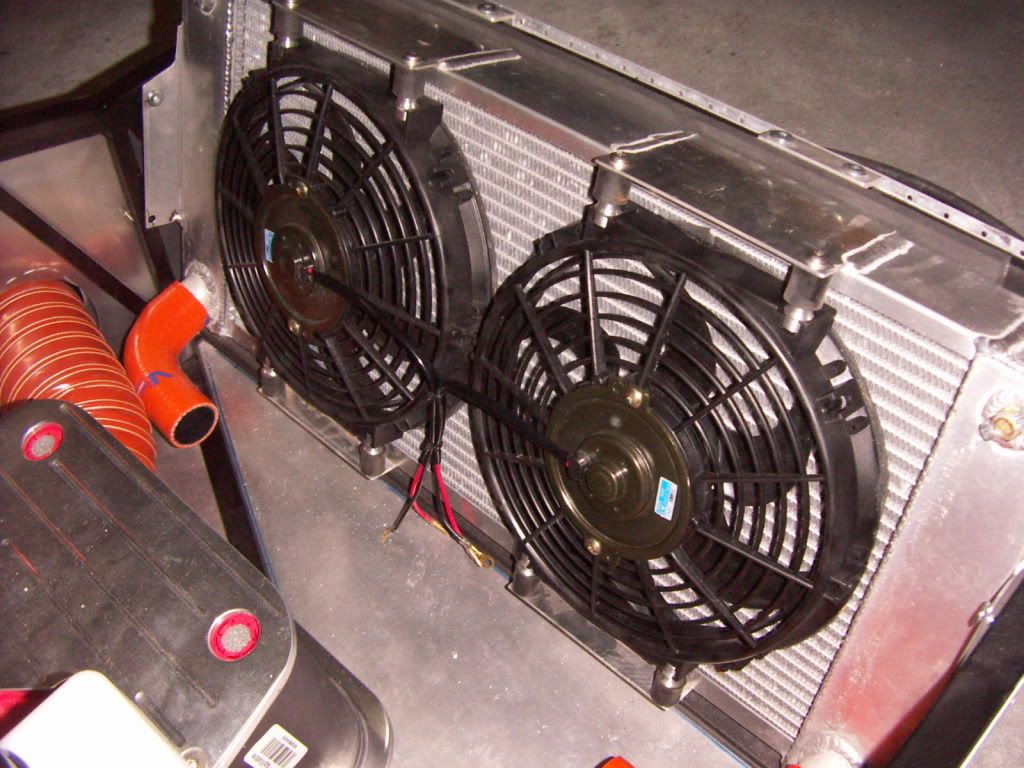
TOM
AWH : 568 h