Joel K
Supporter
The next step on the build was to put the spider and the front clam on the chassis and fab up new radiator brackets.
In order to make room for the power brake booster and the 3.25” deep drop-in fan shroud the radiator needs to be moved forward about 1.25”. Because of this I wanted to double check front clam clearance so needed to place the spyder and the front clam on the chassis.
The good news is the body fits extremely well right off the bat. The wheels fit nicely in the wheel wells and the body gaps are very good.
Also there is enough room under the front clam to place the radiator and fan shroud where it needs to go and clear the power brake booster and master cylinder.
These videos go into some detail how well the body fits at this point and also uncovered an issue with the front tires being too wide. Long story short, wound up replacing the 285/30/19 front tires with 255/30/19. These were the next smaller size available which matched the brand of the rears and these fit much better. I’ll cover
more detail on body fitment in a later post.
Here is a video showing the initial body fitment and checking for clearance of the fan shroud and radiator....
Here is a video of the radiator bracket modification....
Many builders like to better insulate the radiator from vibration. The factory setup may work fine, but I’d rather error on the side of putting more vibration damping in the radiator setup vs. risking damage to the radiator and potential repair later.
I found some inexpensive vibration dampers on eBay that seemed like they would do a good job. They are made to dampen exhaust systems, can withstand high temperatures and come in various colors, I went with boring black, LOL. They use a 3/8” screw, washer, and nut. I’ll probably use 3/8” tube with a smaller screw to mount them.
Here is a link to the ones I purchased....
Here is a pic of the grommets...
Here is a pic which shows how close to the side panels the radiator brackets are and there is little to no room for anything other than a thin grommet which would provide little isolation. Cut a slit in the bracket. Then used a Dremel to carefully cut through the welds....
So the idea is to remove the old brackets and fabricate new ones that sit a little in board which have enough room for the base of the grommet...
4 hours later the brackets were removed and the welds ground off...
Decided to fab the new brackets out of 3/8” x6” x 8” 6061 aluminum plates. This was a lot of work to machine on the mill, but that is what I did. I just really like to mill parts and these took about 8 hours on and off to make. I don’t own a metal brake, but could have quickly made something similar out of 16 guage aluminum with much less effort..
Ground out the center sections....
Then ground out the sides....
Since these brackets sit inboard on the radiator they provide enough room for the base of the grommets...
Drilled some holes where the base of the grommets feed through the bracket. Christmas tree drill bits are great for drilling into thin metal. The brackets were machined to about a 1/10th of an inch thick....
Pic of the radiator and new brackets and grommets placed in the front compartment....
Next step is to fabricate the fan shroud, decide how to attach it to the radiator and have the brackets welded to the radiator. Another step forward...
In order to make room for the power brake booster and the 3.25” deep drop-in fan shroud the radiator needs to be moved forward about 1.25”. Because of this I wanted to double check front clam clearance so needed to place the spyder and the front clam on the chassis.
The good news is the body fits extremely well right off the bat. The wheels fit nicely in the wheel wells and the body gaps are very good.
Also there is enough room under the front clam to place the radiator and fan shroud where it needs to go and clear the power brake booster and master cylinder.
These videos go into some detail how well the body fits at this point and also uncovered an issue with the front tires being too wide. Long story short, wound up replacing the 285/30/19 front tires with 255/30/19. These were the next smaller size available which matched the brand of the rears and these fit much better. I’ll cover
more detail on body fitment in a later post.
Here is a video showing the initial body fitment and checking for clearance of the fan shroud and radiator....
Here is a video of the radiator bracket modification....
Many builders like to better insulate the radiator from vibration. The factory setup may work fine, but I’d rather error on the side of putting more vibration damping in the radiator setup vs. risking damage to the radiator and potential repair later.
I found some inexpensive vibration dampers on eBay that seemed like they would do a good job. They are made to dampen exhaust systems, can withstand high temperatures and come in various colors, I went with boring black, LOL. They use a 3/8” screw, washer, and nut. I’ll probably use 3/8” tube with a smaller screw to mount them.
Here is a link to the ones I purchased....
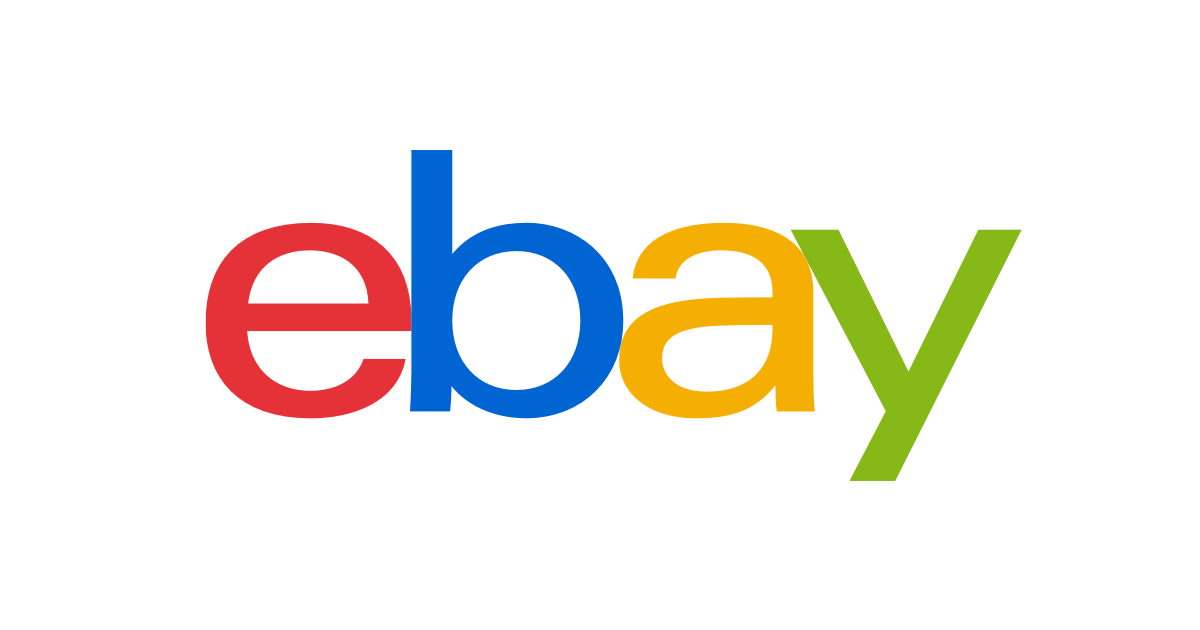
Car & Truck Exhaust & Emission Clamps, Flanges, Hangers & Hardware for sale | eBay
Get the best deals on Car & Truck Exhaust & Emission Clamps, Flanges, Hangers & Hardware when you shop the largest online selection at eBay.com. Free shipping on many items | Browse your favorite brands | affordable prices.
www.ebay.com
Here is a pic of the grommets...
Here is a pic which shows how close to the side panels the radiator brackets are and there is little to no room for anything other than a thin grommet which would provide little isolation. Cut a slit in the bracket. Then used a Dremel to carefully cut through the welds....
So the idea is to remove the old brackets and fabricate new ones that sit a little in board which have enough room for the base of the grommet...
4 hours later the brackets were removed and the welds ground off...
Decided to fab the new brackets out of 3/8” x6” x 8” 6061 aluminum plates. This was a lot of work to machine on the mill, but that is what I did. I just really like to mill parts and these took about 8 hours on and off to make. I don’t own a metal brake, but could have quickly made something similar out of 16 guage aluminum with much less effort..
Ground out the center sections....
Then ground out the sides....
Since these brackets sit inboard on the radiator they provide enough room for the base of the grommets...
Drilled some holes where the base of the grommets feed through the bracket. Christmas tree drill bits are great for drilling into thin metal. The brackets were machined to about a 1/10th of an inch thick....
Pic of the radiator and new brackets and grommets placed in the front compartment....
Next step is to fabricate the fan shroud, decide how to attach it to the radiator and have the brackets welded to the radiator. Another step forward...
Last edited: