I've been encouraged to start a build thread for my project. Its not a GT40 or a replica of anything else for that matter, so if anyone objects and wants the thread removed or moved somewhere else on the forum thats fine by me.
I've been running a blog of sorts for the last year on the car rather than run through the whole history of the thing here if you're interested go browse through the blog and ask questions if you like.
At the moment I'm at the stage where the frame is nearly all together, detail design continues, and I am very much a believer of making the design mistakes in CAD so I tend to flog that to death before cutting metal.
Here's some pictures of the thing, the CAD renderings are a little out of date in some respects but they give the flavor of the thing.
I've been running a blog of sorts for the last year on the car rather than run through the whole history of the thing here if you're interested go browse through the blog and ask questions if you like.
At the moment I'm at the stage where the frame is nearly all together, detail design continues, and I am very much a believer of making the design mistakes in CAD so I tend to flog that to death before cutting metal.
Here's some pictures of the thing, the CAD renderings are a little out of date in some respects but they give the flavor of the thing.
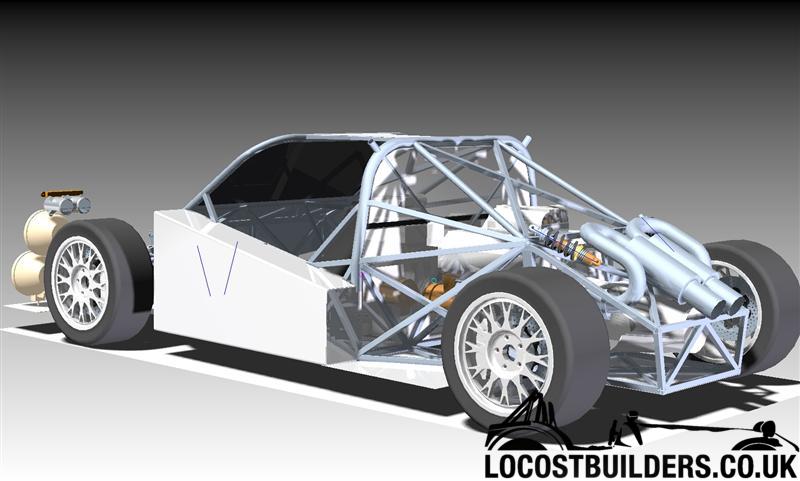
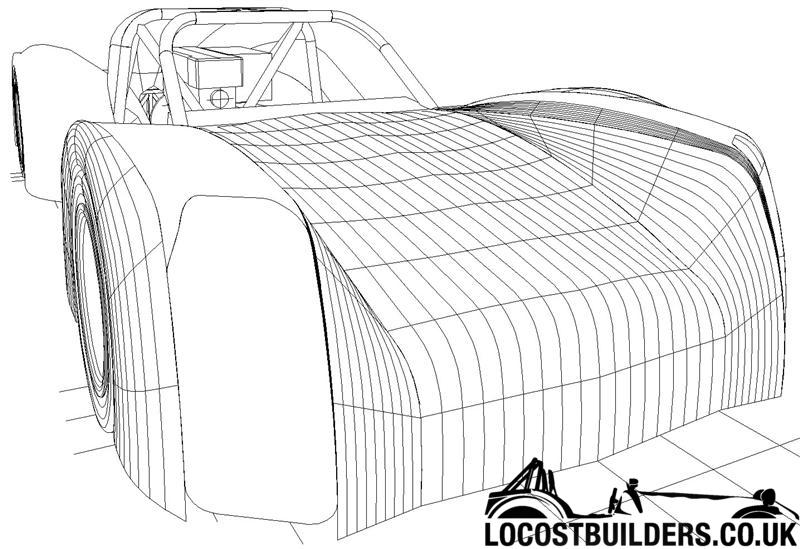
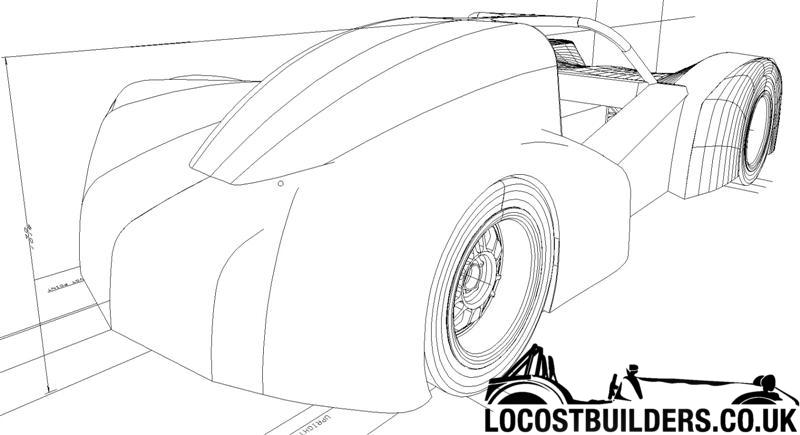