Hi,
Thanks for the comments on my chassis. I started looking into building an alloy chassis about 2 yrs ago, and about a year ago, I decided to build one. I started building my chassis in March this year. Its taken about 200 hours workshop time to get the chassis to its present stage, but I have spent many more hours thinking about how im actually going to build it....
In the tunnel section alone, there is about 450 rivets, I geuss there will be about 3000 rivits in the chassis when its finished...
Jim,
The chassis stiffness, has been the hardest part to achieve, getting the strength isnt difficult, but the stiffness requires a lot more thought and design
For any given chassis design, the stiffness depends on 3 main things
1 ...The stiffness of the material you are useing. ie steel or aluminium
2 ...The amount of it you are useing ie. 0.8mm 1.5mm 2.4mm etc
3....How the material is joined ie ...Riveted... Bonded... Riveted and Bonded...Spot welded...Stitch welded...Fully seam welded
Compared to a GT40, I dont have a steel spider, so I will loose stiffness there, but because I will have a full Roll cage, that will give me that stiffness back
Although my chassis looks similar to a GT40 chassis there are major differences, the GT40 has one large side sponson with ribs. On my chassis, the side sponsons have ribs in them, but the sponson is effectivaly split into 4 different sections, giving it greater stiffness than just one large sponson. The triangulated section behind the seats is in 2 sections, amd also the cross member where the dash sits, is also built in 2 sections.
With all this taken into account, and other design features Im confident my chassis will be as stiff as a GT40 chassis....
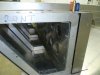
Tom,
The radius rods will attatched to the 50mm x 3mm Virtical box section at the back of the tub, this is where the engine gearbox mounts will attatch to the tub, The engine gearbox, will also be attatched to the back of the side sponsons,( I havnt made these mounts yet ) to spread the loads over a larger surface area. The Roll cage will also attatch to the upper part of the box extrusion, also the inner part of the box will have 1.5mm steel bonded to it, to give added stiffnes, and strength
I have removed the rear part of the triangulated cross member so you can see how it is constructed
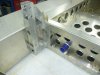
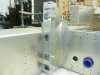