Ed McClements
Supporter
Did some more work on my gearshift, now that I have a rough idea where the gearbox is going to be located. A while back, @peguero posted some nice CAD sketches of the Mk2-style shifter https://www.gt40s.com/threads/original-fav-gt-40-shift-knob-drawings.53501/post-541102
and there's also a pretty clear photo here:-
This will place first gear left-and-forwards, which is what I wanted for my car, so I decided to make a gear lever in the Mk2 style:-
The block of aluminium on the right has been machined to accept the spherical bearing, and will machined further to have three mounting bolts, and be fixed into the firewall just behind the driver's seat.
The two blocks on the left each contain a ball race:-
within which a spigot rotates - 1/2" where it passes through the ball races, and 3/4" where it clamps into the shifter body.
There's still some tidying-up to do, and the rest of the mounting to be fabricated, to allow it to be bolted into place.
I guessed a bit at lengths and ratios, but this gives up to 60mm fore/aft movement on the shift rod which seems plenty, from looking at the gate travel on the UN-1 gearbox.
and there's also a pretty clear photo here:-
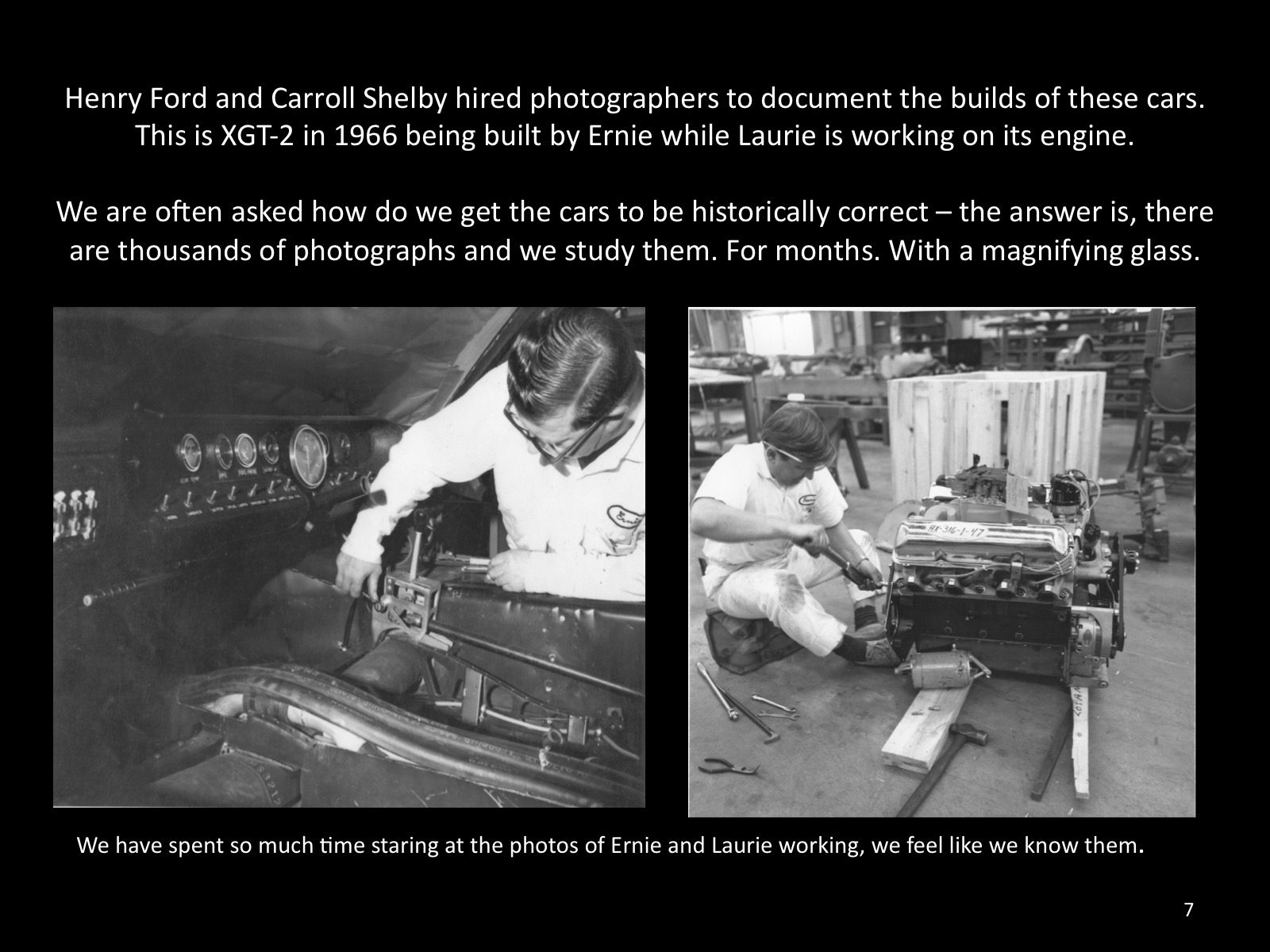
This will place first gear left-and-forwards, which is what I wanted for my car, so I decided to make a gear lever in the Mk2 style:-

The block of aluminium on the right has been machined to accept the spherical bearing, and will machined further to have three mounting bolts, and be fixed into the firewall just behind the driver's seat.
The two blocks on the left each contain a ball race:-


within which a spigot rotates - 1/2" where it passes through the ball races, and 3/4" where it clamps into the shifter body.
There's still some tidying-up to do, and the rest of the mounting to be fabricated, to allow it to be bolted into place.
I guessed a bit at lengths and ratios, but this gives up to 60mm fore/aft movement on the shift rod which seems plenty, from looking at the gate travel on the UN-1 gearbox.